How Can You Make Your Parking Lot Striping Last Longer? 7 Essential Maintenance Tips
Protecting Your Pavement Markings: Expert Strategies for North Texas Business Owners
At Alliance Pressure Washing & Striping, we’ve spent over a decade helping North Texas business owners maximize their parking lot investments. Our experienced team understands that freshly striped parking lots do more than just improve your property’s appearance—they enhance safety, ensure ADA compliance, and create positive first impressions for your customers. While the harsh North Texas elements can be tough on pavement markings, we’ve developed specialized techniques and maintenance protocols tailored to our region’s unique climate challenges. Unlike companies that simply apply paint and move on, we partner with our clients to develop maintenance strategies that extend the life of their striping investments by up to 50% beyond average lifespans. Our commitment to quality materials, proper application methods, and ongoing support has made us the trusted choice for property managers, HOAs, and business owners throughout the region. In this guide, we’ll share professional insights to help you protect your striping investment against the challenging North Texas climate while maximizing its functional and aesthetic benefits.
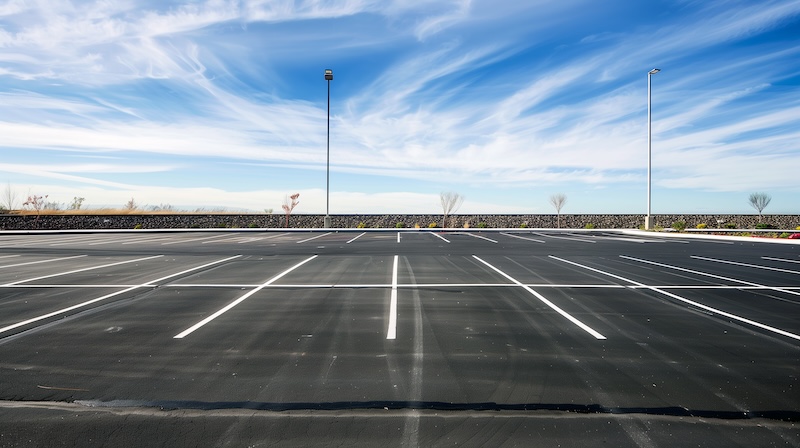
Understanding How North Texas Climate Affects Your Parking Lot Striping
The North Texas region presents unique challenges for parking lot striping durability. Recognizing these regional factors is the first step in developing an effective maintenance strategy.
Our area experiences extreme temperature fluctuations that put significant stress on pavement markings. Summer temperatures regularly exceed 100°F, causing asphalt to expand and become more flexible while accelerating paint degradation through UV exposure. During winter, overnight temperatures can drop below freezing, causing contraction that can crack or weaken striping adhesion. This constant expansion and contraction cycle is particularly hard on parking lots in areas with full sun exposure, which intensifies these effects.
Heavy seasonal rainfall, particularly during spring thunderstorm season, creates additional challenges. The region averages over 40 inches of annual rainfall, with much of it coming in intense downpours that can erode freshly applied striping if proper curing time hasn’t been allowed. Areas with poor drainage, common in older commercial developments, see accelerated striping wear due to standing water that softens paint and reduces adhesion.
High traffic volumes across the area further impact striping longevity. The constant tire friction in busy retail centers around high-growth areas can wear down striping significantly faster than in less-trafficked areas. Studies show that striping in high-traffic lanes deteriorates up to 40% faster than in standard parking spaces, making maintenance particularly important for fire lanes, main thoroughfares, and entrance/exit paths.
Understanding these regional factors allows us to develop maintenance strategies specifically engineered for North Texas’s unique conditions rather than applying generic approaches that might work elsewhere but fall short in our challenging climate.
Essential Maintenance Practices for Extended Striping Life
Implementing these key maintenance practices can significantly extend the life of your parking lot striping investment.
Regular Cleaning with Appropriate Methods
Professional pressure washing of your parking lot surface removes damaging contaminants that break down striping paint. However, the cleaning method matters significantly. We recommend quarterly cleaning using moderate pressure (under 2500 PSI) with specialized surface cleaners that provide thorough cleaning without damaging the striping paint itself. For eco-sensitive areas near local watersheds, we utilize environmentally-friendly cleaning solutions that effectively remove oil and chemical residue without harmful runoff.
The timing of cleaning matters in North Texas—scheduling pressure washing during moderate temperature days (typically in spring and fall) provides optimal results without risking damage from extreme heat or cold. This seasonal approach has proven particularly effective for our clients with properties in high-soil areas where red clay dust accumulation accelerates striping deterioration.
Prompt Oil and Chemical Spill Cleanup
Petroleum products and automotive fluids are particularly damaging to striping paints, as they can penetrate and dissolve the binding agents. For businesses like quick-service auto centers and restaurants throughout the region, where these spills are common, developing a rapid response protocol is essential. We recommend keeping absorbent materials on hand and addressing spills within 24 hours to prevent permanent damage.
For larger commercial properties like shopping centers, implementing staff training for proper spill response can significantly extend striping life in high-risk areas like food delivery zones and near automotive service centers.
Strategic Sealcoating on a Regular Schedule
Applying a quality sealcoat to your asphalt parking lot creates a protective barrier that shields both the pavement and striping from UV damage, water penetration, and chemical exposure. For North Texas properties, we recommend sealcoating every 2-3 years, with properties in full-sun western exposures benefiting from the shorter interval.
Timing sealcoating applications in relation to striping is crucial. For optimal results, we suggest scheduling striping 1-2 weeks after sealcoating application, allowing for proper curing and adherence. This sequencing provides maximum striping adhesion and longevity. Our two-phase approach has helped numerous property managers extend their striping life by 30% or more compared to simultaneous application methods.
Address Pavement Issues Promptly
Cracked or damaged pavement inevitably leads to deteriorated striping. For property owners throughout North Texas, where expansive clay soils create frequent pavement movement, monitoring for and promptly repairing pavement damage is essential for striping preservation. Focus particularly on areas where water tends to pool after our typical heavy spring downpours, as these moisture-prone zones accelerate both pavement and striping deterioration.
For shopping centers and office complexes throughout the region, we recommend quarterly pavement inspections, with special attention following severe weather events like the hailstorms that frequently affect the area.
When and How to Refresh Your Striping
Even with excellent maintenance, all striping eventually requires refreshing. Knowing when and how to approach this process ensures optimal results and value.
Recognizing the Right Time for Restriping
Rather than waiting for complete failure, planning proactive restriping when your markings show approximately 70-80% visibility provides optimal results. For most commercial properties in North Texas, this typically means refreshing high-traffic areas every 12-18 months and standard parking spaces every 18-24 months.
Retail centers in high-traffic corridors often benefit from more frequent partial restriping of high-wear areas rather than waiting to redo the entire parking lot. This targeted approach maintains safety and appearance while managing maintenance budgets effectively.
Choosing the Right Paint for North Texas Conditions
Paint selection significantly impacts longevity in our challenging climate. Water-based acrylic paints work well for standard parking spaces in covered or partially shaded areas common in older shopping centers. However, for areas with full sun exposure or heavy traffic, upgrading to modified acrylic or even thermoplastic markings for critical safety elements like fire lanes and pedestrian crossings provides superior durability.
For properties near airports and along highway corridors where jet fuel residue and higher pollution levels accelerate paint breakdown, we often recommend solvent-based paints that offer better resistance to these specific environmental challenges.
Proper Preparation Makes All the Difference
The preparation process before applying new striping fundamentally affects its longevity. Professional cleaning, proper surface drying time (particularly important during humid North Texas summers), and appropriate temperature conditions during application can extend striping life by 25-40% compared to rushed applications.
For businesses throughout the region that can’t close for extended periods, our team utilizes rapid-dry formulations and strategic scheduling—often working during overnight hours for retail centers and restaurant-heavy areas where daytime disruption would impact business operations.
Protect Your Parking Lot Striping Investment with Professional Maintenance
Don’t let premature striping failure drain your maintenance budget and diminish your property’s appearance. At Alliance Pressure Washing & Striping, our comprehensive maintenance programs are designed specifically for the unique challenges North Texas property owners face. Our team provides expert cleaning, timely maintenance recommendations, and quality restriping services that extend the life of your pavement markings while enhancing your property’s safety and appearance. Contact us today to schedule a complimentary parking lot assessment and learn how our customized maintenance approach can protect your striping investment while reducing your long-term maintenance costs.